Die UV-Härtung stellt eine moderne Lösung dar, um Schutzlacke vom flüssigen in den festen Zustand zu überführen. Diese Materialien bieten eine größere Flexibilität bei der Prozessführung. UV-aushärtende Schutzlacke sind umweltfreundlicher als klassische Lacke, da sie keine Lösungsmittel benötigen, somit lösungsmittelfrei Materialien darstellen.
Klassische Schutzlacke sind mit Lösungsmittel verdünnte Harze.
Erfolgreiche Beispiele für diese Materialklasse sind Bectron® PL 1104 (auf Acrylat-Basis) und Bectron® PL 4122-40E BLF FLZ (auf Alkyd-Polyurethan-Basis).
Lacke bringen einige Vorteile mit sich. Sie sorgen für eine Vorreinigung der Oberfläche durch das Lösungsmittel. Erfahrungen in der Anwendung existieren seit Jahrzehnten. Allerdings werden die Lösemittel zunehmend als Quelle flüchtiger organischer Verbindungen (engl. Volatile Organic Compound, VOC) in Frage gestellt. Zusätzlich wirkt sich die für die Entfernung des Lösungsmittels notwendige Verdampfungswärme negativ auf die CO2-Bilanz des Prozesses aus und verursacht damit zusätzliche Kosten.
Die Aushärtung eines Polymers mit Hilfe von UV-Strahlung ist eine viel erprobte Technologie. Bei vielen Anwendungen ermöglicht die UV-Bestrahlung die vollständige Aushärtung des Materials innerhalb weniger Sekunden.
Eine UV-Härtung erscheint attraktiver, weil sie im Gegensatz zu einer Ofenhärtung oder einer Feuchtigkeitshärtung eine schnelle Verarbeitung und damit kürzere Taktzeiten verspricht. UV-härtende Materialien sind in der Regel frei von organischen Lösungsmitteln (engl. VOC-free); in diesem Zusammenhang wird auch der Begriff 100%- Material verwendet. Der Verzicht auf Lösungsmittel bedeutet auch, dass keine Gefahr für eine Blasenbildung durch Lösungsmittelverdunstung besteht und erübrigt zudem auch eine komplizierte Optimierung des Ofenprofils. Schließlich benötigt eine UV-Anlage weniger Platz in der Fertigungsstraße als ein Durchlaufofen. Wenn die UV-Energie gut genutzt wird und das Material gut konzipiert ist, kann eine bessere Energieeffizienz erreicht werden und damit eine verbesserte Verringerung der CO2-Bilanz.
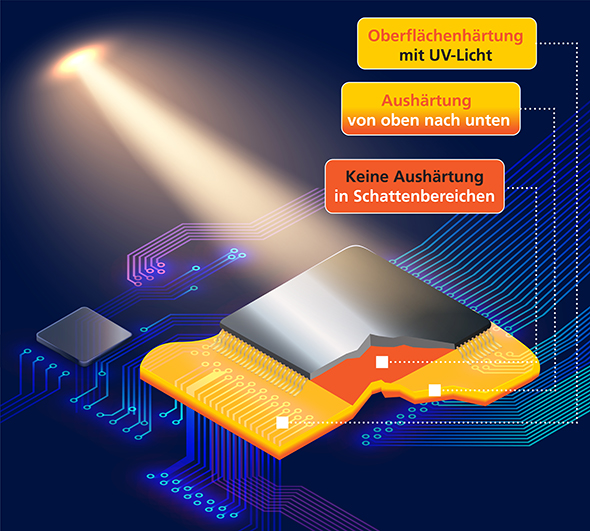
In der Realität sind die Dinge ein wenig vielschichtiger, und die Welt der elektronischen Baugruppen erfordert eine Aushärtung des Materials, gerade auch ohne UV-Licht, insbesondere unter elektronischen Bauteilen wie SMD-Bauelementen, Widerständen, Prozessoren, Kondensatoren oder LEDs-in den sogenannten Schattenbereichen. Um die Härtung in Schattenbereichen sicherzustellen, enthält ein guter UV-härtendender Schutzlack bewusst einen zweiten Aushärtungsmechanismus, dieser wirkt entweder über Feuchtigkeit oder über Wärme.
Die Härtung des UV-Schutzlackes auf einer Elektronikplatine läuft also wie folgt ab:
- Das Material wird unter Gelblicht - frei von UV-Strahlung - mit der Vorhangdüse, durch Sprühventilen, Dosieren oder Pinseln aufgetragen.
- Anschließend breitet sich das flüssige Material auf der Platine aus. Bewusst oder unbewusst gelangt das Beschichtungsmaterial dabei auch unter die Bauteile.
- Dann wird mit UV-Strahlung die Beschichtung belichtet; entweder durch eine UV-Breitbandlampe oder durch eine UV-LED. Die UV-Strahlung löst die Härtungsreaktion aus, die zu einer Fixierung des Lackes auf der Platine führt. Die Aushärtung im Schattenbereich - und je nach Schichtdicke - in größeren Schichttiefen, wird dabei aber noch nicht vollständig umgesetzt.
- Hier kommt der zweite Aushärtungsmechanismus ins Spiel, der entweder mit Hilfe von Feuchtigkeit oder einer Wärmezufuhr den Härtungsprozess abschließt.
Je nach Anforderungsprofil an das elektronische Bauteil in der Praxis werden verschiedene Harzsysteme verwendet. Die Auswahl erfolgt beispielsweise auf Grund des Designs der Platine, der Hochtemperaturbeständigkeit, dem Staubschutz, der Feuchtigkeits- oder Chemikalienbeständigkeit. Diese Anforderungen müssen dann zum Beispiel mit unterschiedlichen Materialeigenschaften wie dem Wärmeausdehnungskoeffizienten und der Materialhärte in Einklang gebracht werden. Einige aktuelle Standardlösungen für UV-härtende Schutzlacke sind in der Tabelle unten aufgeführt.
Produktvorschlag | 2. Härtungs- mechanismus | Typischer Anwendungs- bereich / °C | Viskosität / mPa • s | UL 94 | Härte / Shore | Durchschlagsfestigkeit / kV/mm |
Bectron® PT 4600 | Feuchte | -40 bis 120 | 1 000 | V-0 | A 65 | 20 |
Bectron® PT 4601 | Feuchte | -40 bis 120 | 1 700 | - | A 65 | 20 |
Bectron® PT 4606 | Feuchte | -40 bis 120 | 38 000 | - | A 75 | 20 |
Bectron® PT 4700 N | Feuchte | -40 bis 125 | 150 | V-0 | 116 | |
Bectron® PL 5621D | Wärme | -40 bis 130 | 400 | - | > D 80 | 165 |
Bectron® PL 5622-250 | Wärme | -40 bis 150 | 250 | V-0 | A 85 | 50 |
ELANTAS Europe entwickelt, produziert und vertreibt UV-Beschichtungen auf Grundlage von Acrylaten, Urethanen, Silikonen und Epoxiden.
Die Bectron® PT 46-Serie umfasst eine Produktreihe mit nahezu identischer Chemie, bei der lediglich die Viskosität variiert wird. Dies ermöglicht unterschiedliche Schichtdicken, womit sich alles von einer einfachen Beschichtung mit angepasster Schichtdicke über komplexe Nass-Nass-Prozesse bis hin zu einem Dam-and-Fill-Szenario umsetzen lässt.
Bectron® PT 4700 N weist eine sehr niedrige Viskosität auf, um geringe Schichtdicken von 40 - 150 µm aufzutragen, und ermöglicht damit eine Dünnfilmbeschichtung.
Bectron® PL 5622-250 ist ein UV-härtendes Material auf Epoxidbasis, das eine ausgezeichnete chemische Beständigkeit, eine höhere Hitzebeständigkeit als Acryl/Urethan-Systeme und einen hervorragenden mechanischen Schutz bietet.
Das Bectron®-Team unterstützt Sie gerne bei der Auswahl Ihres Materials: bectron.ELANTAS.europe@. altana. com
Lernen Sie unser Produktportfolio für den Elektronikschutz kennen.